When it comes to woodworking or metal milling, CNC router machines provide a precision that is difficult to replicate manually. A commercial CNC router machine may be financially prohibitive for many, and even if the budget allows, the space required in a typical workshop or garage can be a significant barrier. This is where a DIY solution becomes relevant. However, how do you determine the best plan to follow or which parts to build a CNC router to select?
Different Parts You Need to Build a CNC Router
To build a CNC router, the parts you need depend on different factors in which the purpose you expect is one of them. More importantly, machine parts to build a CNC router must be purchased from reliable sources to ensure quality and robustness. In general, the following parts are the main ones for every CNC router:
Frame
The frame is the backbone of a CNC router machine, providing structure and support for all components. It offers a robust surface for the transmission to exert force and serves as the most prominent feature in an open CNC router machine, with necessary mounting points for various parts.
For optimal performance, a CNC frame must be sturdy and accurately aligned, with precise angles measured down to arcseconds. These angles typically set at 90 degrees establish the machine’s axes, which the software recognizes as fixed.
Various materials can be used for the frame as one of the main parts to build a CNC router, provided they offer sufficient strength and stiffness. While plastic and wood may work for light engraving, they often lack precision for tougher materials.
Cast steel is ideal for heavy-duty applications but is costly and impractical for DIY projects. A hybrid approach, such as using steel tubes for structure and 3D-printed brackets for customization, often yields the best results.
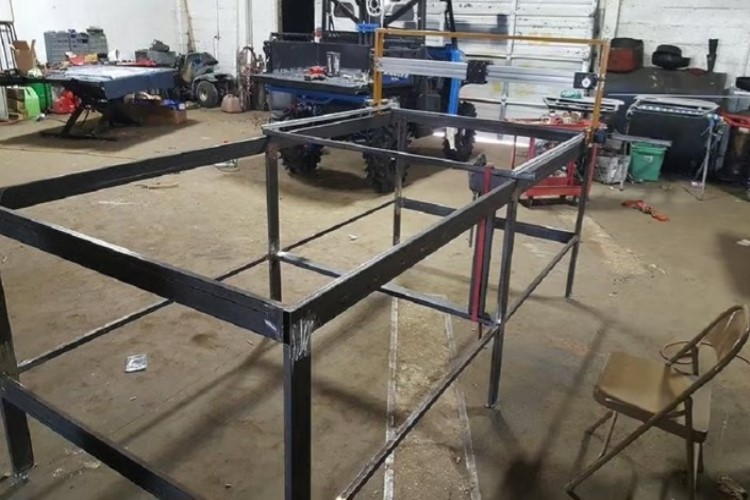
Gantry
The gantry is one of the parts to build a CNC router and its duty is to hold the toolhead above the machine bed and the workpiece. It can either be stationary or mobile, with features that allow for angled cuts. It is common for the gantry to move along the Y-axis while a carriage facilitates the movement of the toolhead along the X-axis.
A solid gantry is essential for precise positioning of the cutting tool. If it is designed to move, it should be lightweight to minimize the energy required for its motion. It also must have a system to supply power to the toolhead, which can be achieved through cable trays, umbilicals, or internal routing. For movable gantries, a mechanism for transferring motion to the toolhead, such as lead screws or belt systems, is necessary.
Typically, the gantry is constructed from the same materials as the machine’s main frame, incorporating rails, slides, or rollers for movement.
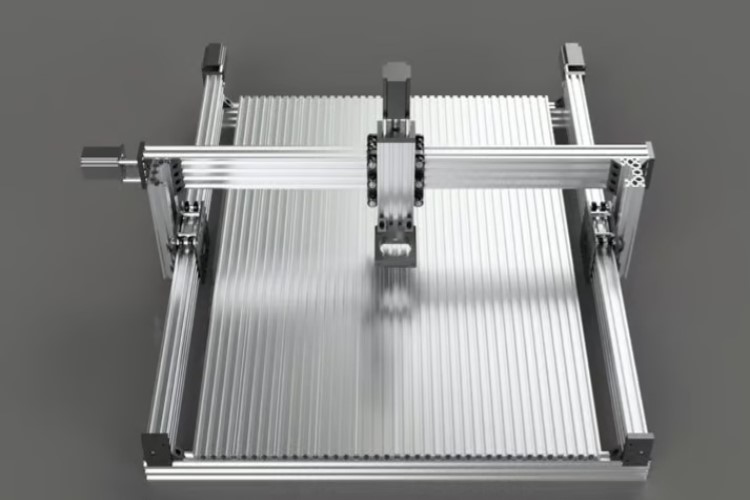
Bed
When we refer to a bed in CNC machining, we’re not talking about a place to sleep! Instead, it’s one of the parts to build a CNC router that secures the workpiece against cutting forces, gravity, and coolant during machining. Besides, it should allow space for the cutting tool to pass through, often achieved with a spoil board or elevated work-holding system.
For precision work, the bed must be flat to ensure alignment. Professional CNC router beds are typically made from cast steel or iron with T-tracks for strong clamping. Alternative materials like MDF, aluminum T-tracks, or grids are also used, each offering unique benefits for different machining applications.
Stepper Motor
Stepper motors are essential parts to build a CNC router for driving the toolhead’s movement relative to the workpiece, generating torque through a system. Larger machinery may require bigger stepper motors or dual motors for each axis.
An effective stepper motor provides adequate torque at high speeds and precise control, but trade-offs must be considered based on specific needs. Key factors include the motor’s size and weight, especially for moving gantries, and ensuring the shaft output matches the transmission system.
For greater precision, servo motors can be considered, as they actively measure and adjust the motor shaft’s position. However, configuring the control electronics for servos can be more complex.
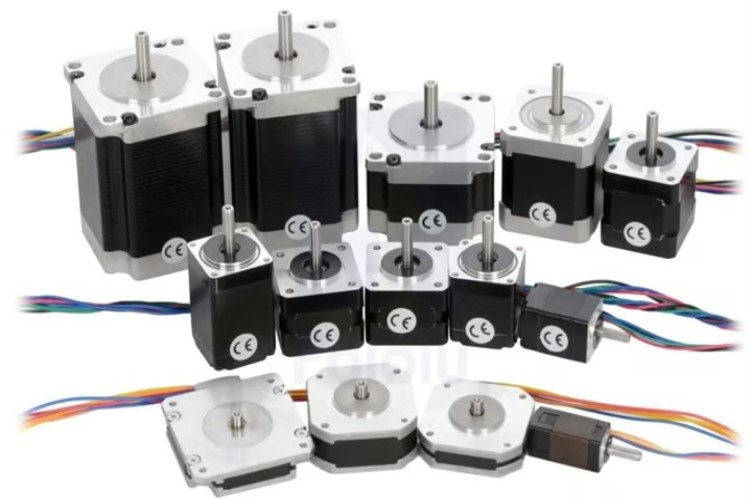
Tool Head
The tool head is the main part to build a CNC router, holding the cutting tool and providing power, usually through rotary motion. To function effectively, a tool head must have a mechanism tailored to the task. For example, a plasma cutter uses a plasma torch, while a water jet requires a nozzle.
Most DIY CNC router setups feature a spindle and chuck, with options ranging from handheld routers to specialized CNC spindles that connect to microcontrollers. The spindle rotates cutting bits, like end mills, to remove material from the workpiece.
Selecting the right tool head for your CNC router depends on your specific requirements. For cutting steel sheets, a plasma cutter is ideal, while woodworking projects typically require a router. Each toolhead has its pros and cons.
Considering cost and complexity, you might opt for a rotary tool head like a router or spindle. If experienced in metalworking, a plasma cutter could be suitable. Electrical discharge machining (EDM) offers precision but poses significant safety risks.
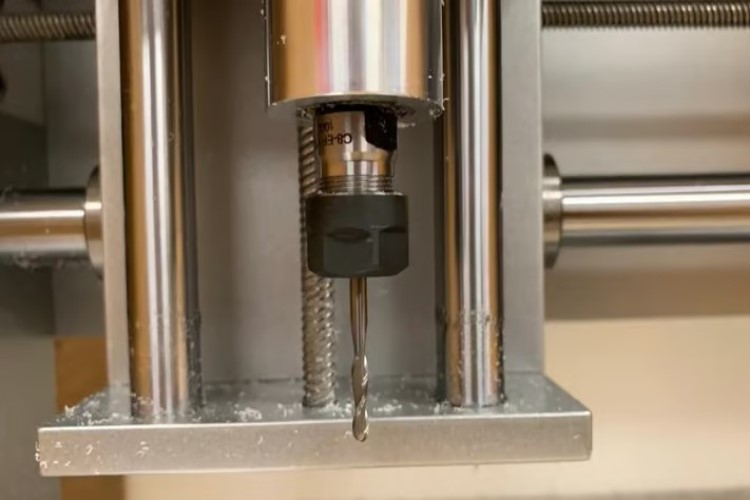
Transmission System
The transmission system, another important part to build a CNC router, converts rotary motion from motors into linear motion of the tool relative to the workpiece, often moving both simultaneously. It includes components that restrict movement to specified axes, such as guide rails, and must integrate well with the frame or gantry.
An effective transmission system should resist deformation from cutting forces, exhibit minimal backlash, and match or exceed the motors’ accuracy. High-precision systems often use numerous small teeth or friction for smoother power transfer.
Choosing the right transmission option depends on the machine’s purpose. For high precision, ball screws are ideal. If slightly less precision is acceptable, lead screws and timing belts are viable alternatives. For applications needing significant power and speed, chain drives can be used, but achieving accuracy may be challenging.
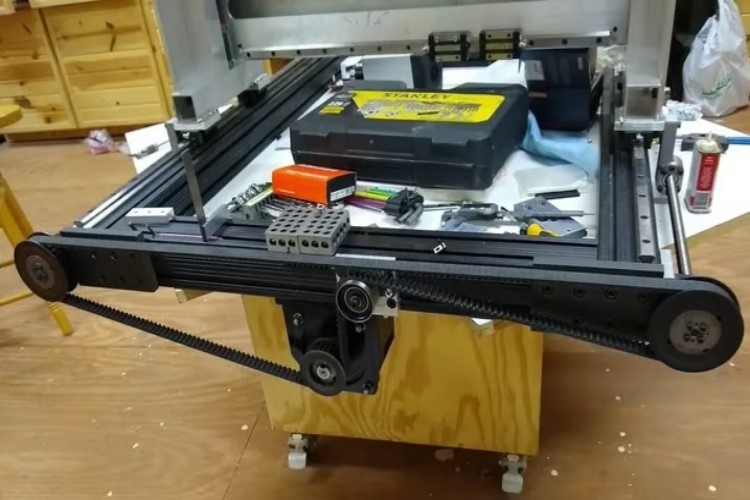
Control Electronics
The microcontroller board plays a crucial role in managing stepper motors and spindles, monitoring end-stop statuses, and translating G-code commands into machine movements. Options range from basic boards to advanced microcontrollers, each catering to different needs. However, compatibility with all firmware and software combinations is not guaranteed.
When selecting control electronics, it’s essential to tailor them to your specific setup. You may need specialized electronics for high-power stepper motors, variable frequency drives for spindles, or servo control systems for precision. Different parts to build a CNC router like end-stops and Z probes are important; while often optional, they can greatly enhance workflow efficiency.
Having these tools can save time and reduce frustration, as they help avoid costly mistakes during operations. Conducting scratch tests to find the material’s top and verifying the G-code to prevent collisions can be tedious without proper equipment.
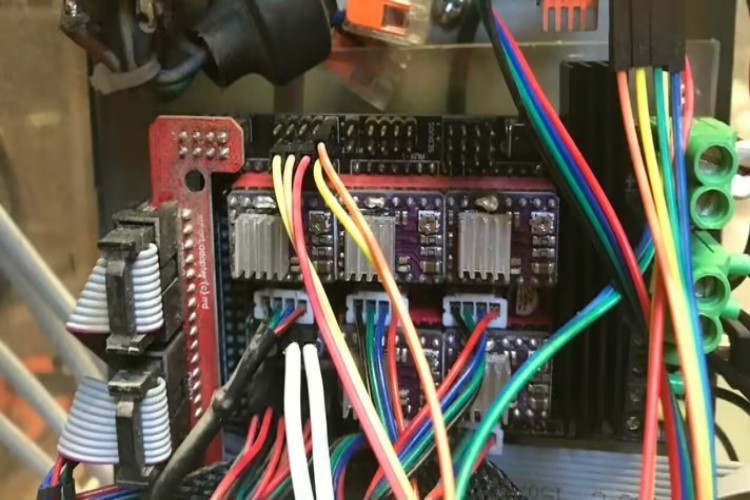
Conclusion
To sum up, you need different parts to build a CNC router including a frame, bed, gantry, stepper motor, transmission system, and control electronics. Investing in the right parts and accessories is vital for a smooth and effective CNC machine experience. However, consulting an expert or purchasing a ready-to-assemble DIY kit are effective solutions for beginners and professionals alike.