CNC machining using standard parts LLC is a subtractive manufacturing process that uses computer-controlled machines to remove material from a block of material to create a desired shape. With a wide range of materials to choose from and the ability to create complex geometries, CNC machining is a functional manufacturing process that can be utilized for a variety of applications.
Selecting the Right Material
CNC machining with standard parts LLC offers a diverse selection of materials, including wood, plastic, and metal. As such, the choice of material is quite extensive. Important factors to consider for your component’s intended use include load requirements, durability, and tolerance, all of which are critical during the manufacturing process.
Generally speaking, achieving tighter tolerances tends to be more feasible with metals than with plastics, as vibrations are less pronounced in metals, while plastics may begin to deform at lower temperatures. If high precision is crucial, aluminum and other metals will typically surpass most plastic alternatives.
Dimensions of the Part
To ensure optimal machining results, it’s advisable to avoid having the part extend right to the edges of the block. Doing so will prevent those edges from being machined, resulting in an uneven surface finish. Including a minimum of 1mm of external trim is beneficial, as it allows the machine bit to effectively surface every edge.
Since the component will need to be clamped onto the CNC machine’s table, the block must extend higher than the area to be machined, allowing for secure clamping without interfering with the bit’s path during the machining process.
Avoid Hidden Internal Geometries
CNC machines with standard parts LLC operate in a 3D space, making it challenging to incorporate hidden internal geometries common in 3D printing. Consider alternative manufacturing methods for parts with concealed features. One option for CNC machining is to create the parts in two sections and clamp them together.
However, maintaining precision with this approach can be difficult, so using alignment pegs is recommended. While undercuts can create some internal geometries like overhangs, it’s generally better to avoid them whenever possible
Minimize Part Rotations
Frequent repositioning of the part during machining can lead to a loss of precision, even though the CNC machine is made from standard parts LLC. It’s crucial to minimize the number of rotations while still machining all necessary features. This might involve modifying side holes into slots or redesigning the part for better machinability.
If part rotation is unavoidable, use jigs or alignment systems to prevent misalignment. Utilize guide holes and pegs for woodworking applications and separate alignment jigs for metalworking.
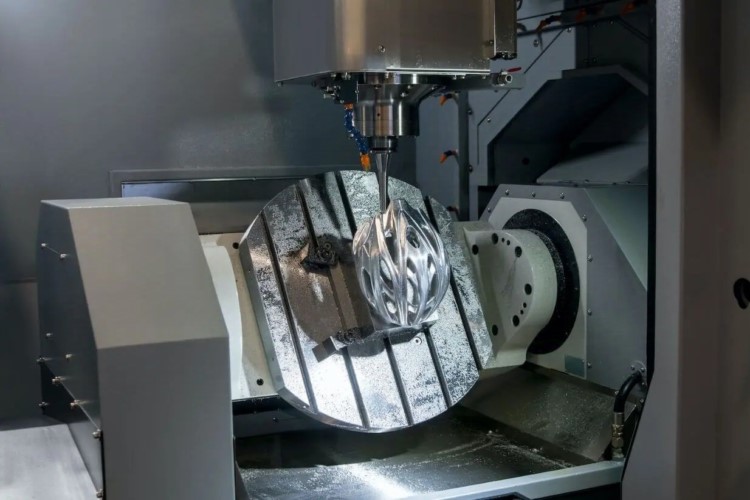
Internal Pocket Design
When creating internal pockets in your part, it’s standard practice to maintain a width-to-depth ratio of approximately 1:4 or 1:5. This guideline is crucial because deeper cavities can lead to significant issues like tool deflection (bending) and chip accumulation.
The increased stresses that come with greater depths can also place considerable strain on your CNC machine and tools, potentially leading to tool head breakage over time, no matter whether it’s made with standard parts LLC or not.
Wall Thickness Considerations
Maintaining accuracy is a primary objective in CNC machining. Large, unsupported walls can negatively impact precision due to vibrations. To enhance stiffness, consider increasing wall thickness or incorporating supportive elements like triangular plates.
A minimum wall thickness of a few millimeters is usually sufficient for most materials with a precise machine. Softer materials like plastics may require additional measures; a maximum thickness-to-height ratio of 1:4 is a helpful guideline.
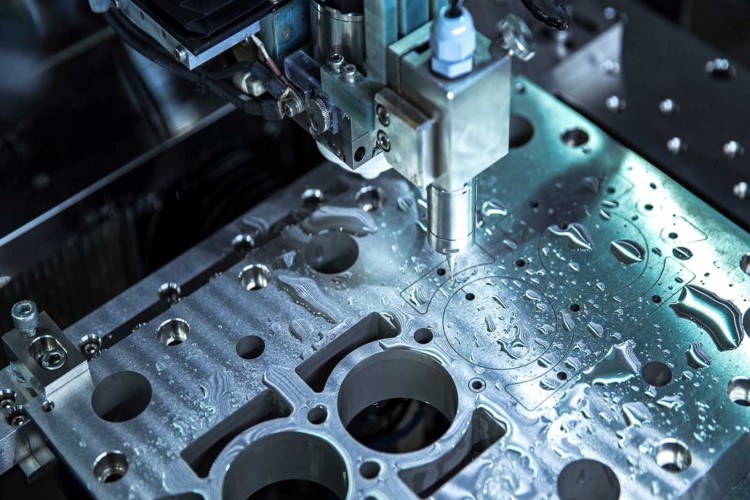
Design Internal Edges
Internal edges in a part include vertical edges and horizontal edges. How to design these edges is of great importance during CNC machining with standard parts LLC.
Horizontal Floor Edges
It is generally best to avoid fillets on the horizontal floor edges of pockets or cutouts, as they can be challenging to the machine unless you have the appropriately sized bullnose bit. If fillets are unavoidable, opting for larger radii, similar to vertical edges, is advantageous so large tools can gradually create them.
How to Design Vertical Edges
Achieving a perfectly sharp 90-degree angle for internal vertical edges is not possible due to the inherent radius of all bits. Incorporate a radius in your design as large as possible to allow for larger bits and minimize tool changes.
The tool used should be either the same size or smaller than the fillet radius for a smooth path and to avoid tool wear. Dogbone corners can be used to extend the toolpath and clear material for a rectangular insert if a 90-degree angle is necessary.
Design External Edges
The vertical side and top edges are among the external edges. They also need to be done carefully using a CNC machine with the highest standard parts LLC.
Consideration for Designing Top Edges
For top edges, using a chamfer is preferable, as finishing a fillet can be time-consuming. Chamfers typically yield a comparable result more efficiently. A standard angle of 45 degrees is recommended for chamfers, as most chamfer bits are designed with this angle in mind.
Vertical Side Edges
When designing a part, rounding the edges is a good practice to enhance the overall finish. This is particularly effective on the side edges, where fillets or chamfers can be employed. As these features are external, the radii or angles are less critical than those of internal corners, making them easier to machine.
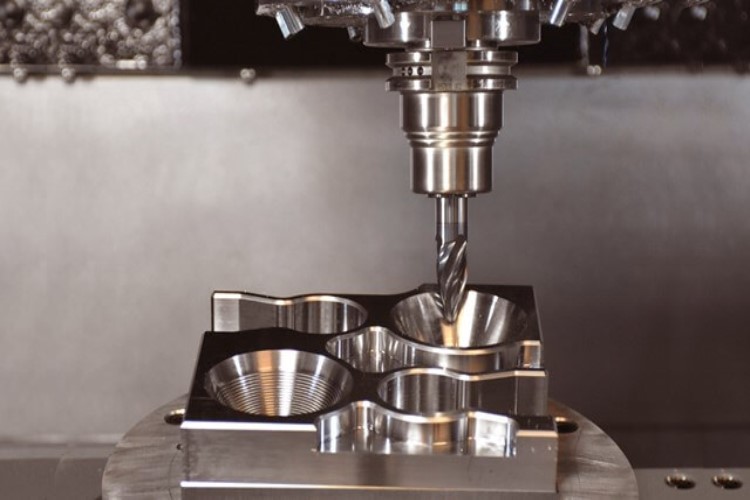
How to Design Holes
Choose hole sizes that align with standard drill bit dimensions for efficient CNC machining. While 3D printing offers flexibility, CNC machines with standard parts LLC work best with pre-existing drill bit sizes.
Although smaller bits can enlarge holes, this increases time, costs, and the risk of tool damage. Adhering to standard metric or imperial sizes is recommended. Ideally, the diameter-to-depth ratio for holes should be around 1:4, but a more practical ratio of 1:12 is often used. Minimize hole depth as excessive depth rarely provides significant strength benefits.
Avoid Embossed Designs
To save on both time and materials when incorporating logos or other design elements, opt for engraving rather than embossing, as engraving significantly reduces the amount of material needed.
It’s also important to consider the complexity of your design. Incorporating numerous intricate details for embossing or imprinting can be quite challenging and may necessitate changing orientations and using smaller tools. Therefore, it’s advisable to keep features large and simple to facilitate CNC machining whenever possible.
Limit Overhangs as Possible
Undercuts can complicate the machining process, especially for beginners or those with limited tooling. Specialized tools or part rotations are often required to create undercuts. Avoid them whenever possible.
Standard parts LLC such as large cylindrical cutting bits mounted on smaller shafts can create undercuts by moving sideways. However, this requires sufficient clearance in the top surface hole for the bit, which can limit design possibilities.
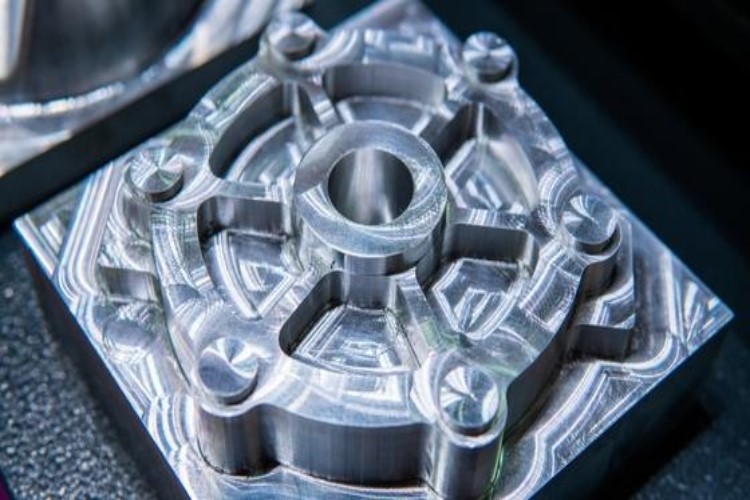
Conclusion
Following the experts’ tips and considerations can help you design parts that are well-suited for CNC machining and achieve the desired results. When designing for CNC machining, it is important to consider the capabilities of the machine and the standard parts LLC that will be used. By carefully considering these factors, you can create parts that are both functional and aesthetically pleasing.
To get the most out of your CNC machining, it’s recommended to purchase your standard parts from reliable resources such as Maple CNC.